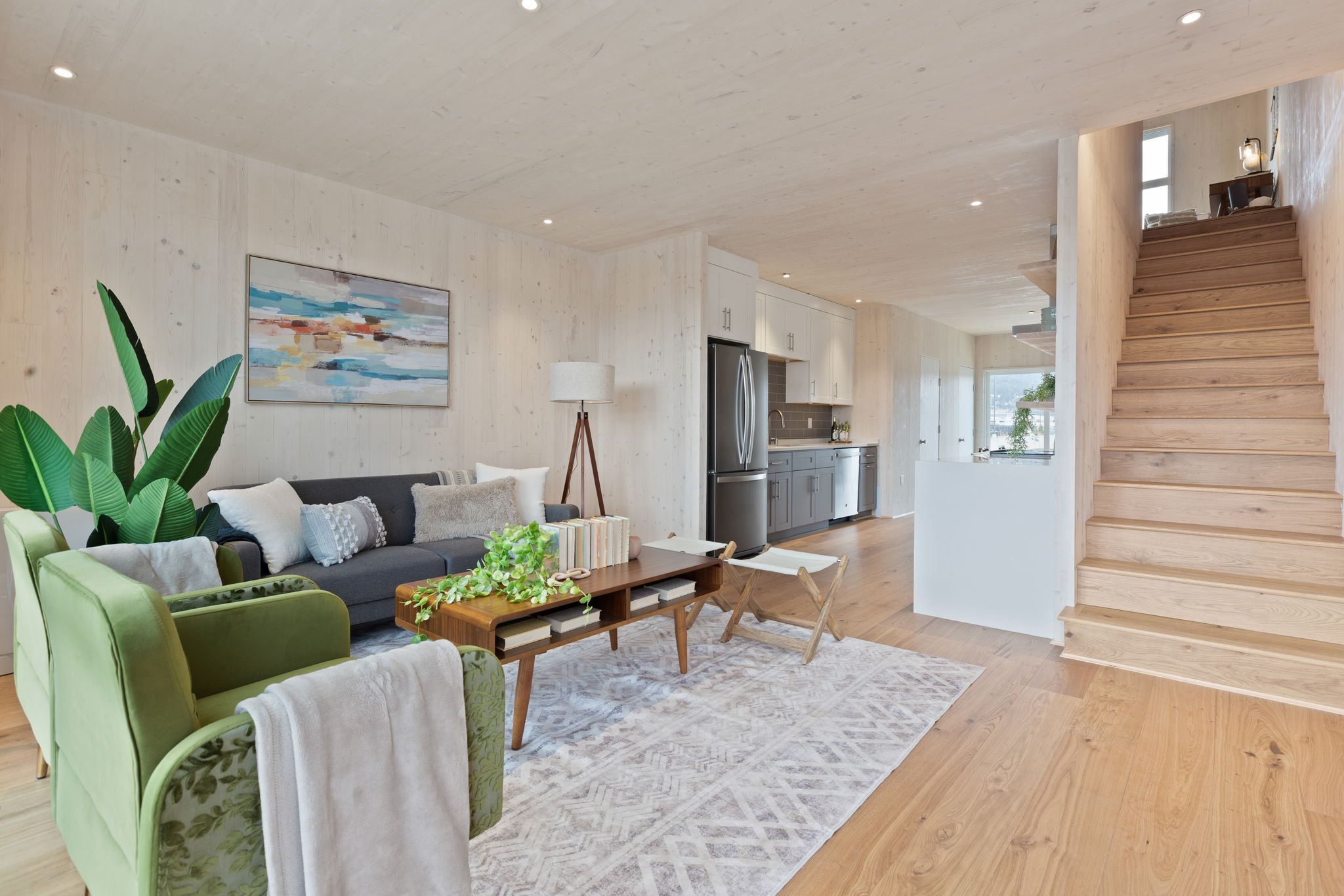

Project Overview
-
A prefabricated building system that:
Allows developers to deliver housing for reduced costs, reduced timeline, and can be manufactured at scale.
Enables enough configurability to meet diversified project needs and be adaptable for modular or flat-pack delivery based on site requirements.
Accelerates the net zero transition with a carbon negative building that integrates into the circular economy.
-
Using new technologies to increase productivity, including standardizing building components, helps modernize housing and the associated workforce.
Off-site manufacturing is a natural progression of sustainable development.
Mass Timber is an ideal material for offsite manufacturing because of its precision manufacturability, engineered structural qualities, and carbon storage.
-
The Mass Timber Model Home is our Integrated Kit, based in our prefabricated building system - testing prefabrication, installation, and logistics.
Components were manufactured off-site and assembled on-site in Spokane, WA.
The 1,200 square foot, two-story + rooftop deck modular home consists of 2 bedrooms and 1.5 baths and is modeled for workforce housing.
Key Learnings:
44% faster than traditional construction
Controls costs with pre-planned and streamlined construction
Avoids weather delays through off-site manufactured modular installation
6.6x more carbon storage than a stick frame home
Less than 100 days from project start to completion
Mass Timber Model Home Timeline < 100 Days
Learn more about our construction technologies and how to partner with us
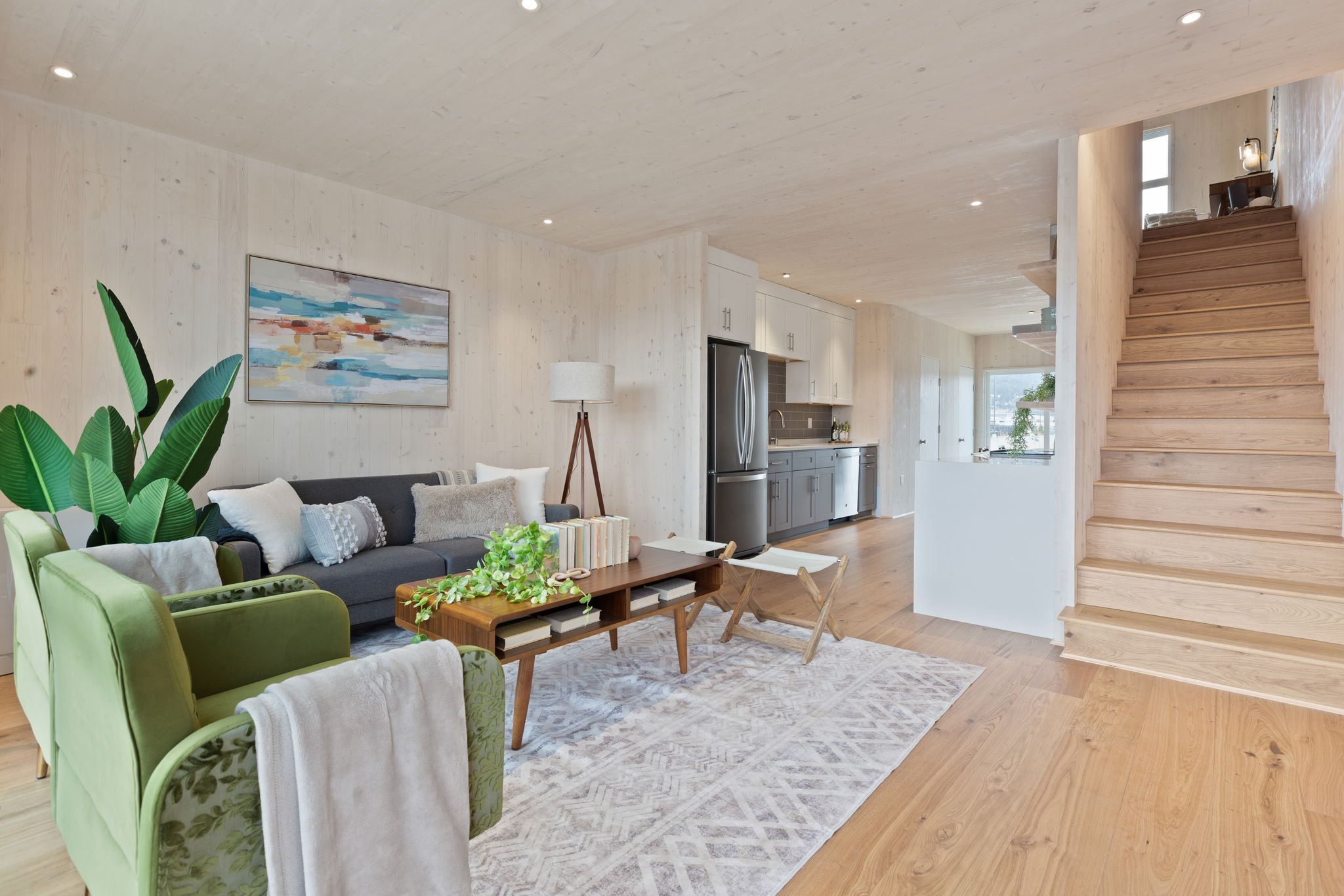



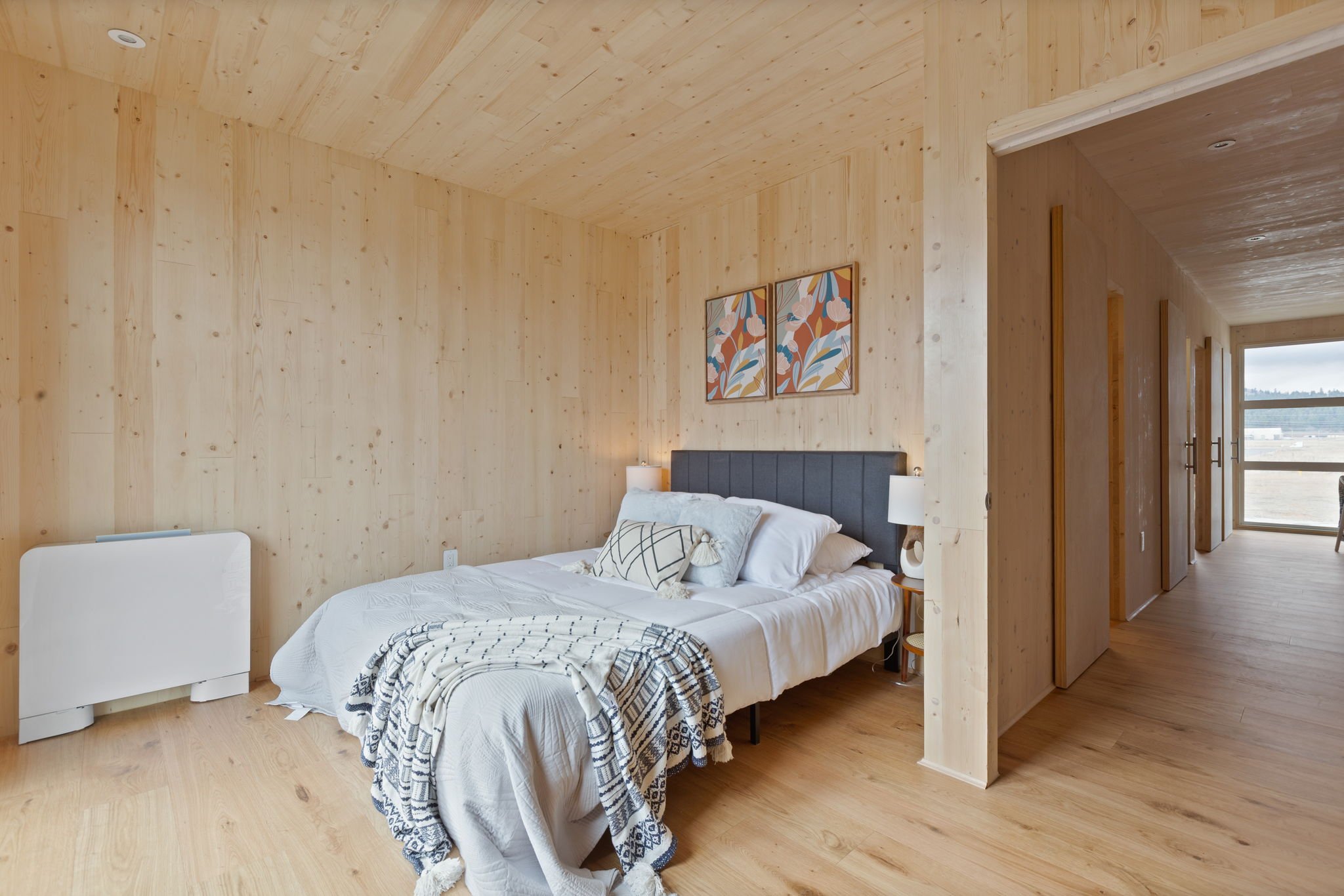


